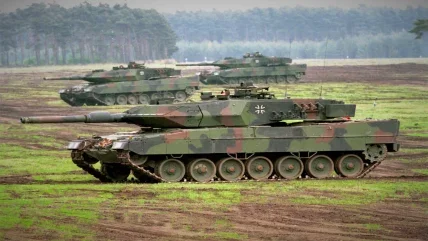
Minimise risk, protect assets and maximise returns on investment: those are the goals of armies looking to leverage advances in robotics to protect valuable soldiers on the battlefield. One such next-generation idea is the use of unmanned vehicles – either remotely piloted or operated autonomously – to distance humans from high-risk situations. The enormity of the task is selfevident and requires a multi-faceted approach. To make a meaningful impact in any theatre, a range of different-sized vehicles with enough commonality between them to deliver cost-efficient operational excellence is required. They also need to be flexible enough to ensure rapidly advancing technology can be easily incorporated into future updates.
At the forefront of this challenge is the US Army’s Next-Generation Combat Vehicles Cross-Functional Team (NGCV CFT). This cutting-edge, tech-driven programme is focused on the rapid development and testing of a suite of three robotic combat vehicles (RCVs) that can step up to a variety of operational tasks. The light and medium RCVs are payload-agnostic platforms that can support a wide range of missions with configurations that can be tailored to the needs of commanders. A third, heavier, RCV is also in development.
Each platform will have a primary mission role, according to Kevin Mills, the US Army’s Ground Vehicle Systems Center’s associate director for robotics. Light RCVs, for example, are designed to “covertly infiltrate to a position of advantage and build situational awareness for a commander, while at the same time reducing tactical risk to the formation”.
The medium RCV, meanwhile, will provide additional manoeuvrability for units thanks to an enhanced direct-fire lethality suite and situational awareness sensors. The heavy RCV remains a work in progress. Its mission and requirements will be defined as the programme continues to evolve, according to Major Cory Wallace, robotic combat vehicles lead for the NGCV CFT.
Purpose-built chassis
The foundation of any vehicle is the chassis, and both the light and medium designs are based on the lighter model’s configuration. According to Mills, this commonality helps facilitate additional mission roles such as obstacle reduction; chemical, biological, radiological and nuclear (CBRN) detection; and anti-armour capability. Previous programmes that marry robotics with field vehicles have taken an ‘upgrade’ approach that integrates robotics functionality into standard designs. “In other robotic programmes, such as the Palletised Loading System, existing army fleet vehicles are being upgraded with [drive] by-wire kits that enable them to be converted into robotic platforms,” says Mills. He says, however, that this is a “fairly invasive” upgrade in terms of boosting the technological capabilities of legacy systems.
Early incarnations of the RCV programme adopted a similar strategy, which was tested on the army’s existing suite of M113 armoured personnel carriers. Results were suboptimal, as Mills explains: “Initial RCV testing used [drive] by-wire-enabled M113 platforms that retrofitted remote actuation kits onto platforms,” he says. “While effective in getting systems into soldiers’ hands quickly, there are limitations with the effectiveness of these surrogates when mechanical failures of the base platform limited availability of the platforms.”
After proving that buying off the shelf does not yet provide optimal outcomes, the US Army shifted its focus to the development of a new base chassis. “The RCV prototypes are purpose-built systems designed specifically to be robots and to allow the army to test the capability of the systems,” says Mills. Designs leveraged from previous government and contractor R&D efforts were applied to the RCV programme to inform the new design. In terms of power, diesel/electric hybrid sources remain in favour as they allow for silent mobility. A full phase-out of diesel isn’t a consideration yet due to operational requirements, though research continues on future fuel sources.
“There is development into leveraging other power sources – such as fuel cells – to replace internal combustion engines in the future,” says Mills. “[But] all-electric is not an option in the foreseeable future due to operational considerations – for example, range requirements and mission-use profiles.”
Open approach
Breathing life into a motorised vehicle and transforming it into a robotic fighting machine without adding to the cognitive burden of soldiers requires heavy use of software and data flow. Pursuing a bespoke vehicles strategy may require a larger design effort, but it can save money over the long run as widely supported interfaces and connectors can be installed upfront. To achieve this, the US Army is maximising the use of open architectures and standard interfaces for its RCV fleet to ensure new technologies can be more easily integrated throughout the programme, avoiding lengthy procurement processes and intellectual property constraints.
“The army is taking a modular open-systems approach (MOSA) across the family of ground robotic capabilities, building off existing small robotic systems,” says Mills. “Effectively, we know the capability we have today isn’t the desired end state, so we’re putting in the proper hooks to enable competition throughout the life-cycle of these platforms.
“This is done through a series of standards, interfaces and government-managed software architectures. The interoperability profile defines the interfaces of robotic systems and enables swapping payloads on the platforms.” Since autonomous systems are software-intensive, that means taking an app-like approach to future development. “This way, we can build off of the common capabilities we have and add or replace software modules that increase capability over time,” says Mills. “Autonomy and robotic control software packages are also leveraging MOSA principles where core software is built on widely adopted frameworks with well-defined interfaces,” explains Mills. That will enable competition at the application layer without requiring changes at the full system layer. The concept is comparable with companies creating new or updated apps for desktop and mobile devices without having to amend the operating system. As the US government closely manages these software interfaces with industrial partners, competition is ensured throughout a system life-cycle, enabling the army to secure “best of breed” regardless of where it’s developed, Mills says. It also enables code reuse.
At the core of the RCV project is a desire to drive the development of autonomous software and behaviours through collaborations with a range of partners across industry and academia. This approach is paying off, with the army currently working alongside various academic institutions, industry partners and other Department of Defense services to develop autonomous software and behaviours. “The MOSA approach has seen more than 40 universities, government R&D centres and industry partners – including both traditional defence sector players and outsiders – become active developers, users or testers of the autonomy software library,” explains Wallace.
To augment external development, the army has launched a ‘software foundry’ to provide software products to programmes requiring ground autonomy and robotic control. It’s a concept that creates a software development capability within the army – a team of soldiers and civilians working in an informal creative environment more akin to Silicon Valley than the military. Creating in-house software expertise is also considered key to future battlefield operations, giving soldiers the capability to respond to software issues themselves on the frontline.
“The military operating environment imposes unique challenges on ground autonomous systems – unstructured environments, off-road operation, GPS-denied, no fixed communication infrastructure to rely on and so on – and that means we can’t just wait for industry to solve this problem for us,” says Mills. “Our approach positions the army to maximise where we do have commonality with commercial ground autonomy, while enabling the army to incrementally solve unique challenges through a soldier-informed agile process.”
Man and machine
At the forefront of any modern software project is AI and leveraging data to maximise outcomes. RCVs are no different. “The army has a robust programme in utilising AI across multiple operational and institutional elements of the force,” says Mills. “AI techniques for both on and off-board learning are being used to improve the ability of systems to detect objects and plan their paths. These are in various stages of development.”
Experimental AI techniques are also being used in aided target recognition, to support crew members in unburdening tasks, for mission planning and to assist in preventative maintenance. “These AI use cases are used to augment human or system performance,” says Mills, but with all key decisions guiding the use of lethal force still falling on the shoulders of the soldier.
Wallace says soldiers are heavily involved in development and testing via “touchpoints” and trials. “After every soldier touchpoint, we analyse our current draft requirements and update them in accordance with the soldier feedback,” he adds.
“Virtual experimentation tools have also been used to put soldiers into video game-like simulations with various robotic capability options to evaluate new tactics, techniques and procedures and provide feedback on what they like and what wasn’t useful.”
Requirements will be kept in draft status until the last possible moment to allow all feedback to be incorporated and to prevent a fixed baseline – something Wallace says will help “deliver the most relevant capabilities to the warfighter”.
And those warfighters won’t have to wait long to benefit from these new machines in the field. After a successful test phase in 2020, the next major RCV exercises will be conducted at Fort Hood, Texas, in the third quarter of 2022, with the first units set to be equipped between 2028 and 2030.
That’s not such a long lead time for a major leap in technology to be developed and tested for the battlefield. The end result will be a flexible family of platforms that provides enhanced operational capabilities and the prospect of dramatically reducing everyday risks for soldiers on the frontline.
UK’s Challenger 3 tanks to enhance land capabilities
While advances in robotic combat vehicles offer great potential to transform the future of land operations, they’re only one of the many elements that Western militaries are embracing in order provide a tactical overmatch against emerging threats like Russia and China. On 7 May 2021, the UK Ministry of Defence (MoD) announced that it had agreed to a contract worth £800m with Rheinmetall BAE Systems Land (RBSL) to deliver 148 upgraded, fully digitised Challenger 3 main battle tanks, with the aim of extending the platform’s out-of-service date to 2040.
The contract is part of a defence review that will see the number of tanks cut down from 227, with these upgraded models entirely replacing the UK’s Challenger 2 tanks, which have been in service since 1998.
“The Integrated Review described a transformed army that will be more lethal, better protected and better connected than any of its comparators,” said deputy chief of the general staff, Lieutenant General Chris Tickell, in that announcement. “Challenger 3 is a manifestation of exactly that change and will sit at the heart of our warfighting capability. Its digital open architecture will ensure that it is integrated across the battlefield, its main armament will overmatch its adversaries and the crew will be afforded a unique level of protection. It is a battle winner.”
The overhaul will include a new 120mm smoothbore gun, a new automatic target detection and tracking system, new thermal long-range cameras as part of an advanced day/night image system, new modular armour, an active protection system, and a turret that is compatible with the tanks of the UK’s military allies.
Each Challenger 3 will also be fitted with a digitised backbone connecting it to the other vehicles in its brigade, enabling data sharing across domains to deliver an information advantage along with multi-domain integration, providing an edge over opponents. In the same announcement, Major General Darren Crook, director of land equipment for the MoD’s defence equipment and support (DE&S) department, said: “This is a significant step forward for defence and UK industry as we continue to develop and modernise our fleet of land vehicles, and I am looking forward to working closely with our industry partners to deliver the very best capabilities we can for the British Army.”
Ultimately, the Challenger 3 represents a significant generational upgrade in capability for the British Army and will play a key role in its attempts to provide a tactical overmatch against emerging threats in the years to come. Designed to take part in multi-domain warfare, its modular design offers an enhanced survivability suite capable of taking on any opponent that it is likely to encounter, underpinning the UK’s credibility in the land domain.