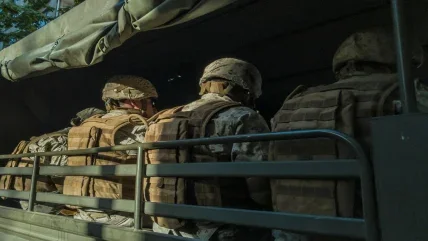
Over recent decades, rugged electronics have revolutionised how militaries go about their work. From unmanned vehicles to tablets they can grab from their backpacks, these devices are helping troops become more effective warfighters, sharpening logistics and boosting their lethality.
Certainly, these trends are reflected in the numbers, with one estimate suggesting that the market for rugged electronics will enjoy growth of 7.4% through 2028.
Yet if rugged electronics are becoming key to armies the world over – the US Department of Defense recently invested $154m in new electrical systems – challenges remain. Perhaps the most obvious problem is the question of cables and connectors, the wires fundamental to all electronic devices. Often more vulnerable than other parts of a machine, an exposed wire or loose connector can ruin even the most rugged of systems. Even so, the situation is far from hopeless. By investing carefully in the right materials and the right designs, experienced cable manufacturers can craft machines that work flawlessly, and even under the most difficult and testing conditions – as one Minnesota company is readily proving.
“Omnetics has developed its Nano-D range of connectors, developed to meet or exceed MILDTL- 32139 requirements.”
Sophisticated new technology
Cables and connectors are fundamental to all electronics – and rugged military devices are no exception. Moving power and signals from one part of a machine to another, they’re vital everywhere from unmanned vehicles to rugged laptops.
More to the point, the increasing sophistication of military hardware is making cables even more important.
Consider, for instance, the case of advanced helmets. Allowing soldiers to spot allies or get directions via GPS – with the relevant information beamed to a digital screen in front of their eyes – the helmets gather data from a variety of sources. Boasting new circuitry, process boards inside the helmet convert various types of analogue and millimetre data into digital information. From there, each module is linked, via miniature (so-called ‘nano’) cables, to master units inside each machine.
It’s a similar story in other technical areas too, with military radios and laser-targeting devices just two of the technologies now boasting deeply integrated digital systems, a fact that inevitably requires cables and connectors to effectively acquire, store and retrieve relevant data.
It goes without saying, of course, that these cables must also be light and compact enough to ensure devices remain portable on the battlefield – all while also being robust enough to cope with everything nature and the heat of battle throws at them.
Nor is this a merely hypothetical issue. Connectors are often the weakest link of any rugged technology, with the incursion of dirt or damp potentially fatal to the device. Quite aside from the security worries here, any breakage also has financial consequences: with some military radios now costing around $20,000, unreliable connectors can quickly prove expensive.
Connectors for every occasion
Omnetics is well-placed to answer these challenges – and more. Based in Minneapolis, and with decades of experience in connector design and manufacture, the company has worked with military officials in the US and around the world.
In practice, Omnetics achieves this through customisation – carefully developing its equipment with a particular device in mind. Take, for instance, its connectors for ground-troop electronics. With users splashing through rivers and darting into muddy foxholes, the connectors for these machines need to be tough. Omnetics, for its part, battles to ensure they are, covering cables with flexible, waterproof polyurethane jacketing, helping connectors meet IP-67/68 specifications.
This spirit of flexibility extends to the work Omnetics does on unmanned vehicles. Moving at speed, often on bumpy terrain, any connector must be designed to ‘hold tight’ during travel.
For this reason, Omnetics designs its pin to socket connectors with care, using tempered beryllium copper, as well as nickel and hard gold (plated to ASTM B488 standards), to meet shock and performance specifications.
In a similar vein, the company typically uses screws and jacks to keep connectors in place, and mitigate the tremors that UAVs undergo while in flight – a process known as ‘fretting’ and which risks damaging cables.
As those references to industry standards imply, moreover, Omnetics can offer a bespoke service thanks to its clear understanding of customers’ needs. Nano-D connectors provide a good example of what performance can be achieved through a miniaturised connector. Based on a pitch of 0.635mm, (.025 inch), these devices are only a quarter of the volume and have 80% less mass than the MIL-DTL-83513 Micro-D connectors they supersede.
Technical innovations
Yet if Omnetics is a firm built on specificity, it’s equally clear that many of its connectors share common features. Probably the most striking is their size. In a sector increasingly predicated on flexibility – and the number of units helmets and other sophisticated machines now include – troops need equipment that’s both small and reliable.
To that end, Omnetics has developed its Nano-D range of connectors. Developed to meet or exceed MILDTL- 32139 requirements, these devices are both portable and light. Apart from being easier to transport, their lower mass helps protect circuits from shocks and vibrations, especially important for unmanned vehicles.
In fact, Omnetics’ Nano-D connectors are so robust that they are even suitable for space travel, sealed as they are with low-outgassing polymers that are capable of even meeting NASA’s most exacting specifications.
Considering the military satellite industry is already worth $56bn, such investments surely make sense – and speak vividly to how Omnetics keeps ahead in an evolving market. Together with other innovations, for example developing ‘next generation’ connectors that can offer higher power where needed, it seems clear that Omnetics has its eyes on tomorrow in other ways too. Given everything the company has achieved so far, that’s surely just as well.
To read the white paper on the Evolution of Portable Military Electronics click here.