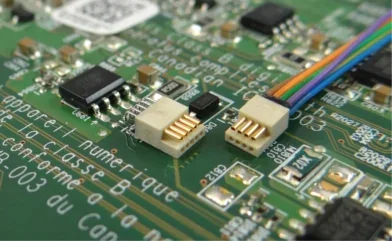
Phased array communication systems are revolutionising connectivity, offering unparalleled reliability, bandwidth and low latency. As demand for these systems surges, so does the need for high-volume designs that cater to diverse industries.
Omnetics’ approach to high-volume design
Low Earth Orbit (LEO) satellite constellations, with their high reliability and low latency, are fundamental to modern phased array communications. These constellations rely on numerous interconnected satellites and advanced phased array antennas that utilise thousands of miniature antennas and sophisticated algorithms to electronically steer signals. This steering is a significant leap from the older, mechanically-steered Geostationary Orbit (GSO) satellites. Eric Bergquist, project engineer at Omnetics, highlights this shift: “This wasn’t needed when GSO satellites were the main method of communication, as all of the tracking was slow and could be done mechanically. However, mechanical systems are more expensive and prone to failure than the fully solid-state and electronically-controlled phased array antenna.”
Omnetics recognises the critical role of high-volume design in meeting the growing demand for these phased array communication systems. “Due to the many benefits of phased array communications, it is being implemented widely in many different applications,” says Bergquist. “This means the production volumes for these systems are quite high compared to other projects requiring ultra-high-reliability.”
To maintain its competitive edge, Omnetics prioritises continuous improvement and innovation. “To compete for these contracts, Omnetics needs to look at each project and implement any design changes or improvements that will allow us to provide a lower unit cost and to get product out the door faster,” Bergquist explains. “This also involves designing the product to facilitate faster and more efficient integration into the customers’ systems.”
Central to Omnetics’ high-volume design strategy is the use of many smaller modules interconnected through a backplane. This modular approach not only simplifies manufacturing but also enhances production efficiency. Bergquist elaborates on the benefits of this approach: “The first reason (or drive perhaps) is that traditional array systems are very large, so it is impractical to manufacture the antenna as a monolithic system. The second is that, much like wafers for computer processors, the likelihood of fallout is proportional to the area of the board being manufactured. By manufacturing smaller modules, a lower percentage of them will have to be discarded due to manufacturing errors.”
The growing trend of solder-inplace solutions
In addition to modular design, Omnetics has embraced solder-in-place solutions as a robust and reliable method for board mounting. “One of the critical requirements for high reliability applications is having a strong connection to the PCB,” says Bergquist. “These connectors will potentially see significant stress in their life, including launching into space, rough handling in the field, and so on.”
Solder-in-place technology offers several advantages. It provides a strong connection to the PCB, comparable to traditional threaded fasteners, while also being amenable to automation, which reduces manual labor and potential errors. Bergquist explains, “For almost all common highreliability connector standards, the highstrength PCB retention solution is to have a screw thread into the connector through the PCB and be torqued to allow a strong connection. However, this process requires a lot of manual labor and is prone to error. Solder-in-place solutions seek to provide PCB retention strength similar to threaded fasteners but using only solder-based processes that can be performed automatically on the PCB assembly line.”
Implementing solder-inplace solutions
There are two primary ways to implement solder-in-place solutions: through-hole mounting and surface-mount technology.
Through-hole mounting is generally favoured for its superior strength. This method involves drilling holes through the PCB, plating the walls of the holes and soldering the connector’s solderable posts into the holes. While this process can be prone to errors such as solder paste squeezing through the hole or not wetting the entire wall surface, Omnetics has developed solutions to mitigate these issues, including attaching solderable posts into standard threaded holes in Nano-D and Micro-D connectors, which allows them to convert their COTS products into solderable solutions. Surface-mount solutions offer greater ease of implementation in production lines. This method involves soldering the connector to flat metallic pads on the surface of the PCB. To ensure a strong and reliable connection, it is crucial to make the retention solder pads as large as possible. For high-reliability surfacemount connectors, the most common strategy is to solder directly to the metal shell for the retention connection.
Omnetics provides a range of solutions for both through-hole and surface-mount implementations, underscoring its commitment to meeting diverse customer needs. For surface-mount connectors, Omnetics often utilises gold plating to provide a high-quality surface for the solder to wet onto. To facilitate this, some connector shells are designed with ‘feet’ that increase the soldering surface area and provide a wider base which can resist higher forces.
Bringing it all together
The applications of phased array communication systems are diverse and continue to expand. Some of the key areas where this technology is making a significant impact include commercial aviation (providing in-flight Wi-Fi for passengers), military aviation (enhancing communication capabilities for military aircraft), navy communications (improving ship-to-ship and ship-to-shore communication), and space communications (enabling highbandwidth communication between spacecraft and ground stations).
High-volume design is crucial for meeting the escalating demand for phased array communication systems. Omnetics’ dedication to providing innovative and costeffective solutions, coupled with its focus on modular design and solder-in-place technology, positions it as a leader in enabling seamless connectivity for a wide array of applications.
As phased array technology continues to evolve, Omnetics remains committed to pushing the boundaries of high-volume design, ensuring that its connectors and cable solutions meet the ever-increasing demands of this dynamic field.
To read the white paper on the High-volume design in phased array communication systems click here.